动车组车头玻璃钢底板常见故障及优化方案分析
分类:列车资讯
发布时间:2025-04-15 04:06:10
动车组车头部使用的玻璃钢底板可能会遇到哪些常见问题?是否还有改进空间呢?
为了确保动车组底部整体结构平滑且设备舱密封性良好,需要在车头下方凹陷处进行封闭处理。通常采用轻质的玻璃钢材料制作该部件,并通过16个M10×40螺栓将其紧固于适当位置。
经过大约20万公里的运行后,在检查过程中发现多个螺栓安装孔周围出现了裂纹。
这种玻璃钢底板尺寸为1268mm × 925mm × 6mm,重量约为16.56kg。由于该部件体积较大,在中部使用了截面为6mm×20mm的网状玻璃钢加强筋以增强整体刚性。
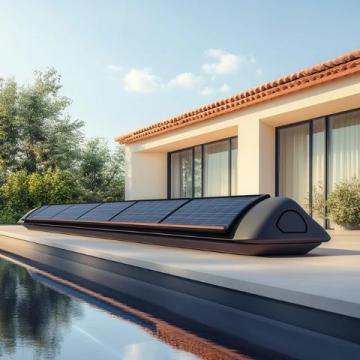
在四周设有16个直径为12毫米的螺栓孔,并且为了提高安全性,底板上预埋了40mm×40mm×2mm不锈钢垫片来增加连接处的压力承受能力。具体结构如图所示。
关于玻璃钢底板故障的原因分析
在调查过程中发现,所有的裂纹都出现在螺栓紧固位置,并且通过进一步的检查和分析得出结论:裂纹起源于不锈钢垫片与玻璃钢粘合处。
1. 制造工艺分析:
- 首先制作出6mm厚的整体玻璃钢底板,然后在脱模后开孔定位。接着需要对预埋的不锈钢垫片进行打磨处理,确保其平整无瑕疵。
- 然而,在实际制造过程中,往往会出现边缘不齐或锐角等缺陷,这会进一步增加应力集中现象,导致最终裂纹产生和扩散。
针对上述问题,提出了几种优化设计方案:
- 改善施工工艺: 将预埋的不锈钢垫片替换为衬套,并简化安装流程,不再需要打磨玻璃钢底板表面。这样可以消除螺栓孔周围的纤维不连续现象,从而避免制造缺陷。
- 提高整体刚度: 进一步优化设计,在连接区域将厚度从6mm增加到8mm;同时将中部的矩形网状加强筋替换为更复杂的梯形结构(50mm×30mm×10mm),使用泡沫芯材来增强强度。
- 降低应力集中: 在螺栓孔周围增设U型不锈钢梁,以增加受力面积并重新分配紧固力,从而消除应力集中现象,并减少对底板的损害。
通过HyperWorks有限元软件进行仿真分析和地面疲劳强度试验验证了优化设计的效果。结果显示:新结构不仅提高了玻璃钢底板的整体刚性,还大幅降低了螺栓孔周围的压力水平,可靠性得到了显著提升。
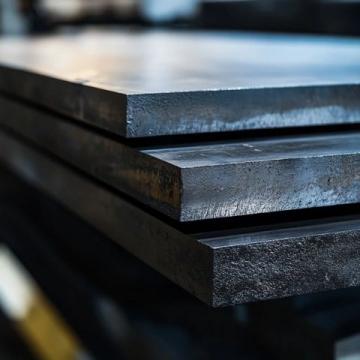
实施效果: 优化方案应用于车辆后,在超过120万公里的运行里程内未发现任何裂纹问题。相比之下,原设计在大约20万公里时便开始出现问题,证明了新结构的安全性和可靠性都有了明显改善。
本文通过详细分析玻璃钢底板故障的原因,并从多个角度提出改进措施,最终验证了优化设计方案的有效性,解决了该部件存在的安全隐患,确保列车运行更加安全可靠。
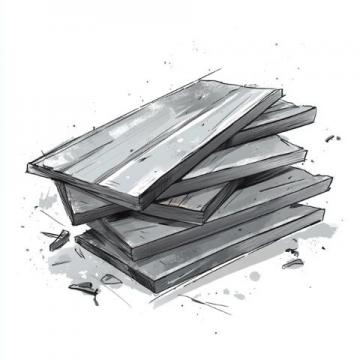